There has been a slight easing in material shortages over the past month with lead times for some products starting to settle down according to the Construction Leadership Council (CLC).
The national wave of home improvements during the pandemic sparked a huge demand for materials like fencing, decking, paint and cement. The domestic repair, maintenance and improvement sector reports that the market now shows signs of levelling off after this spike, and this includes homeowners’ own DIY projects. The temporary upturn in people relocating and moving is however expected to keep Britain’s builders busy for years to come as people look to personalise and improve their new homes.
The CLC’s product availability working group which meets monthly to record and analyse materials demand and supply, hopes this will give the materials supply industry some breathing space. Joint Chairs of the group, The Builders Merchants Federation Chief Executive John Newcomb and the Construction Products Association chief executive Peter Caplehorn, issued a statement.
They warned the supply chain was “just about managing under unprecedented circumstances” and that the industry was in a better position than it was four months ago. But they warned contractors were “not out of the woods yet”. They say that shortages of bagged cement eased last month as new supplies were brought in from abroad, although extended delivery times are still likely to continue until the end of the year.
Supply and demand of course affects cost. The price of some imported sawn or planed timber jumped 23 per cent between June and July, according to the latest data provided by the Government. Several key materials remain in short supply, including timber battens, chipboard, steel lintels and PVC products. Bricks and blocks are still a concern, with some regions seeing increased delays. Some concrete roof tiles are still seeing very long lead times, averaging around 24 to 30 weeks.
The national shortage of HGV drivers is of course adding to these delays as distribution of products is taking far longer than usual. Global shipping capacity has been reduced by 25% since the start of the pandemic and this is also having an impact.
Finally, rapidly rising energy prices are now affecting manufacturing. In the steel industry, the doubling of the wholesale cost of gas has led to some UK steel plants temporarily stopping production.
The price of materials in the future remain difficult to predict due to the cost and availability of raw materials and continued issues with labour and transport. Naturally these delays and price increases will have an impact on domestic extensions, conversions, and alterations, and on construction professionals working in the RMI sector. Small building companies are impacted the most by these delays and increases and they don’t have the resources and buying power that the national house builders have.
Homeowners are looking at delaying their projects in the hope that materials may come down in price, but this is impossible to predict with any accuracy. Some builders are reported to be asking for additional payments at the end of the job to cover the extra costs they’ve incurred. Others are suggesting substitutions for different finishes and products, but this increases the risk of not complying with planning conditions or building regulation requirements.
This crisis looks set to continue for the foreseeable future.
Read other articles
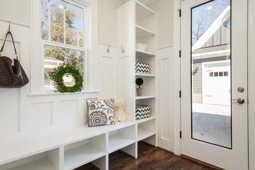
Builder’s total price higher than the original estimate? – Ask Anna Question of the Week
Read article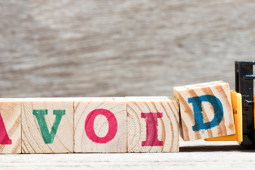
10 home renovation problems owners can avoid
Read article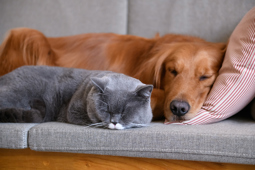
10 things you can do to improve your home
Read article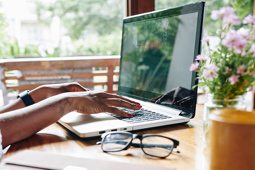