Dear Anna
I’ve been asked to get a drain test done for my extension. What does that involve and who can do it?
A drain test should be carried out on any new or modified lengths of drain, above or below ground, to make sure the pipes are properly connected and don’t have any leaks.
Why do I need to do this?
The requirement for drain testing is set out in the Building Regulations and can be found in Approved Document H sections 1.38 and 2.59-2.62, with further guidance in BS 8000 Pt 13, BS EN 752, and BS EN 12056.
Your building control surveyor will probably want to witness the test being carried out in person (they don’t do it for you) although they may accept third party certification. Don’t confuse a drain test with a drain survey. If you can’t provide evidence of a satisfactory drain test it will hold up the issuing of your Completion Certificate.
It's sensible to carry out drain tests before the drain run is covered over as you don’t want to discover a leak when the job is finished – it's much better to test as you go. Building control needs a test at completion in case the drain has been damaged during the course of the work. Unfortunately, it's not uncommon for cement, plaster, paint, or solvents to be tipped down drains during construction, which can block or damage the pipes and joints.
If your drainage includes air admittance valves be aware that these are difficult to test so it's preferable to test before you fit them – and remember they can fail over time so it's best to provide a permanent access point rather than tiling over them.
Anyone can carry out a test, but you do need to borrow, hire, or buy specialist equipment including bungs/stoppers and gauges.
Photo credit: martinplanthire.co.uk
There are two main methods of carrying out a drain test, an air test, or a water test:
Air test (only for pipes up to 300mm diameter)
This is a fast and efficient way to make sure your drains are working as they should be. A specific part of the drain is separated off using airtight plugs or bungs, and a gauge or manometer is used to check the pressure. This is set to 110mm head for five minutes. Next, the pressure is adjusted to a 100mm head reading and after 5 minutes any change in head is measured. The test is detailed in BS EN 1610 and in Approved Document H.
This method can’t be used on all kinds of drains and systems, as it relies on the drain being able to be blocked at both ends and is extremely sensitive to temperature change. For example, a reduction in temperature of just 1 degree inside the pipe can be enough of a drop for the test to fail.
How do you carry out an air test?
To begin with, fit a bung at the head of the pipe run with the correct nipple cap to attach it to the hose that will be connected to the manometer. Make sure that your manometer has been partially topped up with water (actually milk is easier to see) prior to this.
After this, use a hand pump to increase the pressure until the manometer reads between 125-150mm. After this is completed it’s important to leave the equipment for 10 minutes in order to let everything settle before reducing the manometer’s pressure to 110mm.
Next, the manometer must be monitored for five minutes, and within this time it must not drop below 75mm. This will be considered a pass, however, if it does reduce to below the 75mm line on the manometer there should be an examination for leaks and other signs of failure. If anything needs rectifying this must be completed before conducting another test and if this fails move to a water test.
Water test. (only for pipes up to 300mm diameter)
Water testing, also known as water drop testing, is a method of testing drains that requires less pressure but, unlike the air test, takes a few hours to set up as you need to let the water settle. The test itself works by bunging up the two ends of a system, filling the system with water, and monitoring the water levels either at a manhole or access point. Using a water test means that you can test the whole system at once which reduces the amount of time your surveyor needs to spend on your site and also limits the time the drains can’t be used.
How do you carry out a water test?
For pipes up to 300mm diameter, the system should be filled with water up to a depth of 5m above the lowest invert in the test section and a minimum depth of 1m measured at the highest invert in the test section. This may then be left for a period (one hour is generally sufficient) to condition the pipe. The test pressure should then be maintained for a period of 30 minutes, by topping up the water level as necessary so that it is within 100mm of the required level throughout the test. The losses per square metre of surface area should not exceed 0.15 litres for test lengths with only pipelines or 0.20 litres for test lengths including pipelines and manholes, or 0.40 litres for tests with only manholes and inspection chambers alone (i.e., no pipelines).
Other methods include smoke testing and the mandrel testing method. All of the tests are conducted to ensure that the newly installed plumbing system is free of leaks and is up to standard. You may need to use several different drain testing procedures to test the whole system.
What if there are leaks?
It is not uncommon to find leaks and need to undertake repairs after running a drainage test. Often, it may be a case of a faulty length of drainage pipe or a joint that may need re-doing or sealing. However, if there is no obvious fault you may need to disassemble the whole system and individually test each section using an air test. Once you’ve found and rectified the fault, you’ll need to run the overall test again.
When you are testing manhole covers and inspection chambers, it is common for joints to leak but is usually an easy fix through the process of re-joining and resealing. However, it may be a structural problem with the base and the concrete with the sealing of the pipe. If this is the problem and epoxy mortar doesn’t fix it, the only option is to completely rebuild, which is not ideal but necessary in accordance with regulations. Once again always retest after attempting to rectify any faults within the system.
- Connectivity- Where separate drainage systems are provided the connections should be proven to ensure that they are connected to the correct system.
How can I check the condition of my drains?
CCTV Drain Surveys
A CCTV drain survey is an in-depth inspection of the condition of drainage systems. A high-tech camera records video footage inside the drain and captures useful information that drainage engineers can use to identify any issues that might be present like blockages or root damage in pipes or sewers. An engineer will use specialist survey equipment (waterproof cameras, access rods, crawlers, and sonar units) to gain access to your drains and insert the CCTV camera, providing a real-time view of your drains so they can inspect the condition of your drains and identify blockages or damage. It’s advisable to have the condition of your drains surveyed before and after work.
Photo credit: London-drainage.co.uk
Remember that most drainage alterations, including installing a new toilet, relocating a kitchen, or creating a new shower room require Building Regulations approval. Check with your local authority building control team before you start work.
Read related articles on Front Door
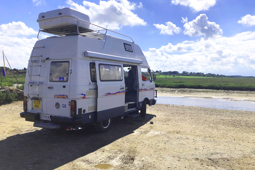
Introducing Anna from Ask Anna
Read article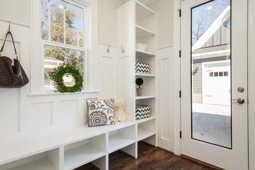
Builder’s total price higher than the original estimate? – Ask Anna Question of the Week
Read article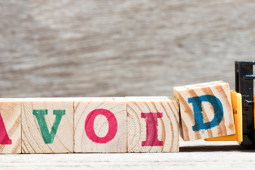
10 home renovation problems owners can avoid
Read article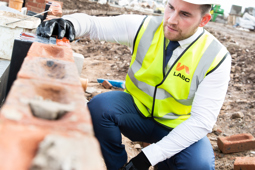